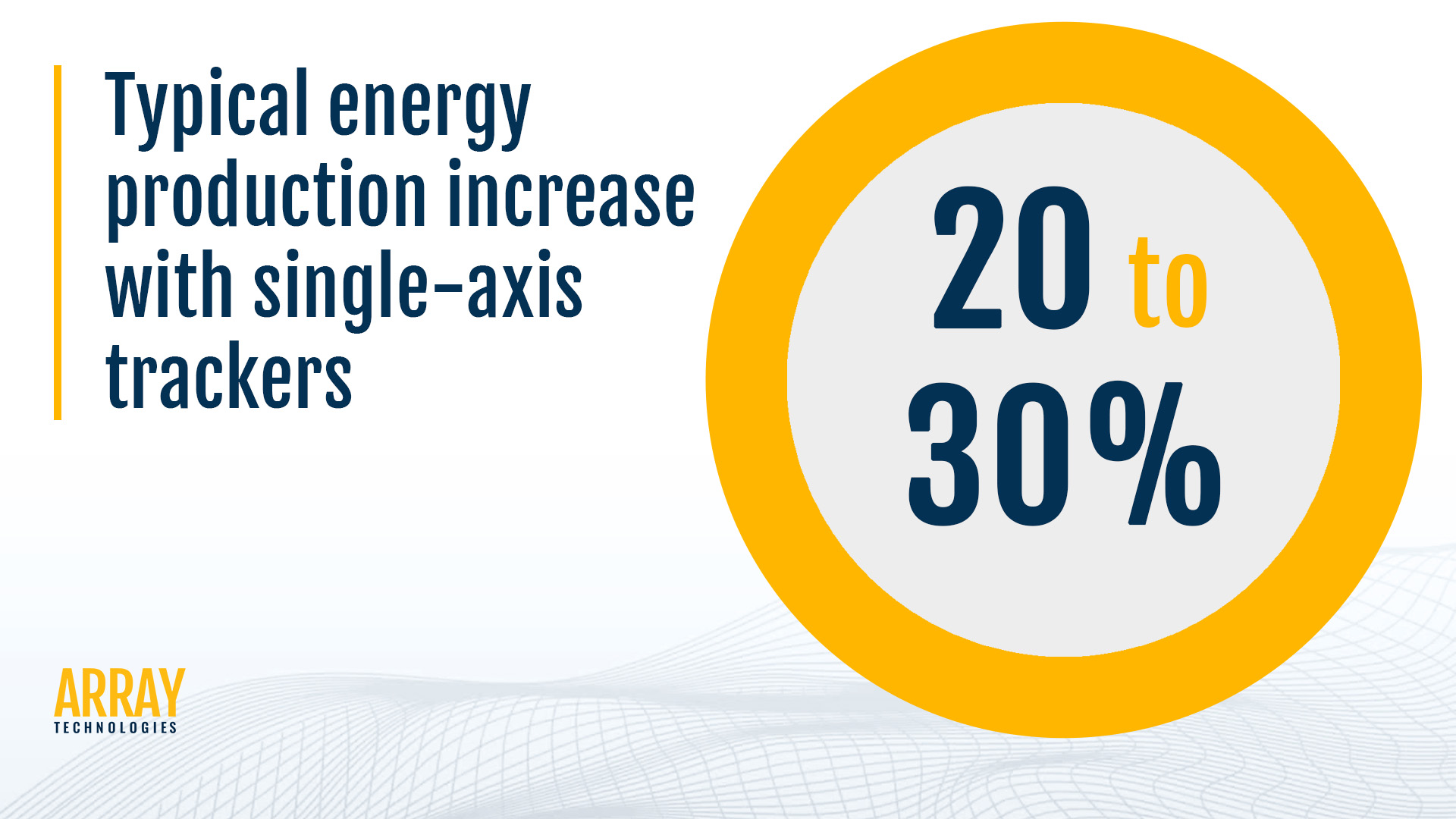
Every aspect of the PV solar project plays a part in risk. Plant design, available technology, and risk mitigation features that can be built into a tracker can affect all elements of a solar assets long-term risk profile.
Trackers are one of the major inputs of the risk equation. In this final post of our 3-part series on risk mitigation for investors and insurers, we’ll talk about trackers and risk over the long term.
Trackers are integral to lower financial risk
In the past, more conservative investors and insurers have questioned trackers as a possible risk. With using anything that requires mechanical parts to move, there’s always the fear that those parts could cause problems. In which case, there’s more initial cost and disappointing payouts should the trackers fail, diminishing power production and cash flow.
Trackers, like most things in the PV industry, are under constant scrutiny and development. Now it’s widely accepted that a well-built tracker properly installed on a properly designed site will far outperform fixed-tilt sites in levelized cost of energy (LCOE).
As utility site sizes increase and PPA prices fall, the margins for energy production returns tighten. Read more about falling PPA prices in our previous post on market risk assessment.
Large utility-scale sites can’t afford to not have trackers. The repositioning to keep panels capturing light during the critical morning and evening hours may seem incremental, but it adds up. Energy production typically increases 20 to 30% with single-axis trackers.
The benefit of additional energy with trackers can be millions of dollars on average-sized solar sites. Of course, not just any tracker means lower long-term financial risk. Material quality, drive mechanism, ease of install, and maintenance should all be considered.
Why modern trackers are smarter
Machine learning algorithms can now map out PV sites and respond intelligently. This is a huge advantage in real-world settings where tricky terrain, weather variation, and differing module configuration can throw variables into energy output calculations.
The addition of software, such as SmarTrackTM by ARRAY Technologies, gives trackers an edge that can add up to 5% more production under diffuse light conditions and on challenging terrain.
Across undulating terrain, machine learning can boost the amount of light trackers capture even more by meeting incline percentages with an equal percentage in energy production. For example, production can be increased 1% on a 1% incline, 2% on a 2% incline, etc.
Weighing CAPEX and OPEX of PV sites
The more reliable the components, the lower OPEX costs over time. Lower OPEX is one of the major predictors in a more financially rewarding PV investment. All equipment requires some maintenance over its lifetime but minimizing routine O&M costs as well as break fixes is one of the most impactful financial risk aversion strategies.
The TUV study we referenced in the first post of this series also concluded that durability and ease of repair outweigh upfront equipment costs. Data is stacking up in favor of investing more CAPEX in quality equipment for lower OPEX and better return over the long run.
Lenders and insurers can also ask developers to provide data using predictive analysis tools like PVsyst or PlantPredict. Of course, as with any data tool, it’s absolutely critical that these software platforms are being used correctly.
Without a thorough knowledge of the software, default inputs can lead to drastically different outcomes from reality. Small variations between actual site conditions and the selected information can alter energy estimations considerably, leading to disappointed stake holders.
The use of legacy data sets including on-the-ground knowledge of site idiosyncrasies, similar plants performance in similar locations, geographical historical yield data along with predictive analysis should all be part of the decision making.
With the appropriate investment of both time and money into CAPEX upfront, long-term issues ranging from sites design flaws to component failure reduces OPEX over time and increases functionality and financial returns.
Site design is foundational to success
No other “fixes” make up for poor design. The integrity of the site as a whole comes from a solid foundation. Tenants of good design include:
- Don’t simply “work with” your site terrain. Take advantage of it. Use it as a way to improve system performance. You can do this by capitalizing on any terrain already facing the sun and choosing a tracker with high tolerances that can handle the slopes and topography. This is how your design aligns with your objective to capture the most sun.
- Choose quality components that will have the most uptime over the lifetime of the plant. This includes hardware built to withstand extreme weather such as wind and hail. Trackers should be robust enough to last 30 years or more and have a field-proven track record of doing so.
- Add machine learning software to your toolset. Modern trackers benefit from the integration smart solutions, which learns the optimal path and pacing to capture more light.
- Prioritizing plant resiliency and uptime is perhaps more important than any other strategy including software for optimizing energy output. If you have optimizing software, but your equipment is not working, what good will the software do? This applies to all components across the site from trackers to modules to inverters, etc.
Choose the appropriate PV modules for your site. Specifying modules that can withstand shading, which can be unavoidable on some sites, is often a basic tenant of good site design.
ARRAY trackers vetted, tested, and reliable
A feature of ARRAY Technologies trackers that makes them such a touchstone in the industry is the centralized drive mechanism. This patented, innovative design drastically reduces parts count and makes ARRAY trackers more robust and reliable.
We’ve developed our tracking system using solid hardware and fewer parts. Specifically, ARRAY trackers have over 160 times fewer components than trackers with a decentralized architecture. Without extra parts prone to failure such as monitors, sensors, and batteries, we’ve drastically reduced weaknesses and cut the risk of profit-draining downtime and expensive insurance claims due to damage. Also, they’re easier and faster to install.
ARRAY specializes in trackers easily used on all types of terrain. Our trackers are used in projects with EPCs, developers, and site owners all over the world. To date, more than 22+ GW of ARRAY Technologies trackers are deployed worldwide.
We test extensively through modeling and testing in the field, as well as through third-party engineer evaluation. We do this to make sure the results are valid and not the product of a company echo-chamber.
No single solution for minimal risk
Again, no one product or method can deliver a strong solar production site. There are several pieces to a solid overall risk mitigation strategy.
Investors see better returns on capital with an awareness of all these elements and by insisting on minimizing risk through quality. Similarly, insurers can develop policies with confidence knowing this comprehensive perspective is followed.
It’s no surprise, but the best way to ensure this awareness and quality is to perform due diligence. We hope this blog series was an informative look at these topics, and we encourage you to dig further into the available data.
A good place to read more on this topic is from RINA, who includes more than two years’ worth of research on this topic in a recently released report. It’s a thorough assessment of CAPEX versus OPEX and minimizing downtime for lower risk and higher returns.
Download our white paper “Wind and Hail Risk Mitigation and the Firming of Commercial Insurance Markets for Utility-Scale Solar Power Plants” to learn more about our patented passive weather risk mitigation technology and how we can help reduce your weather risk.
Click here for other articles by this author