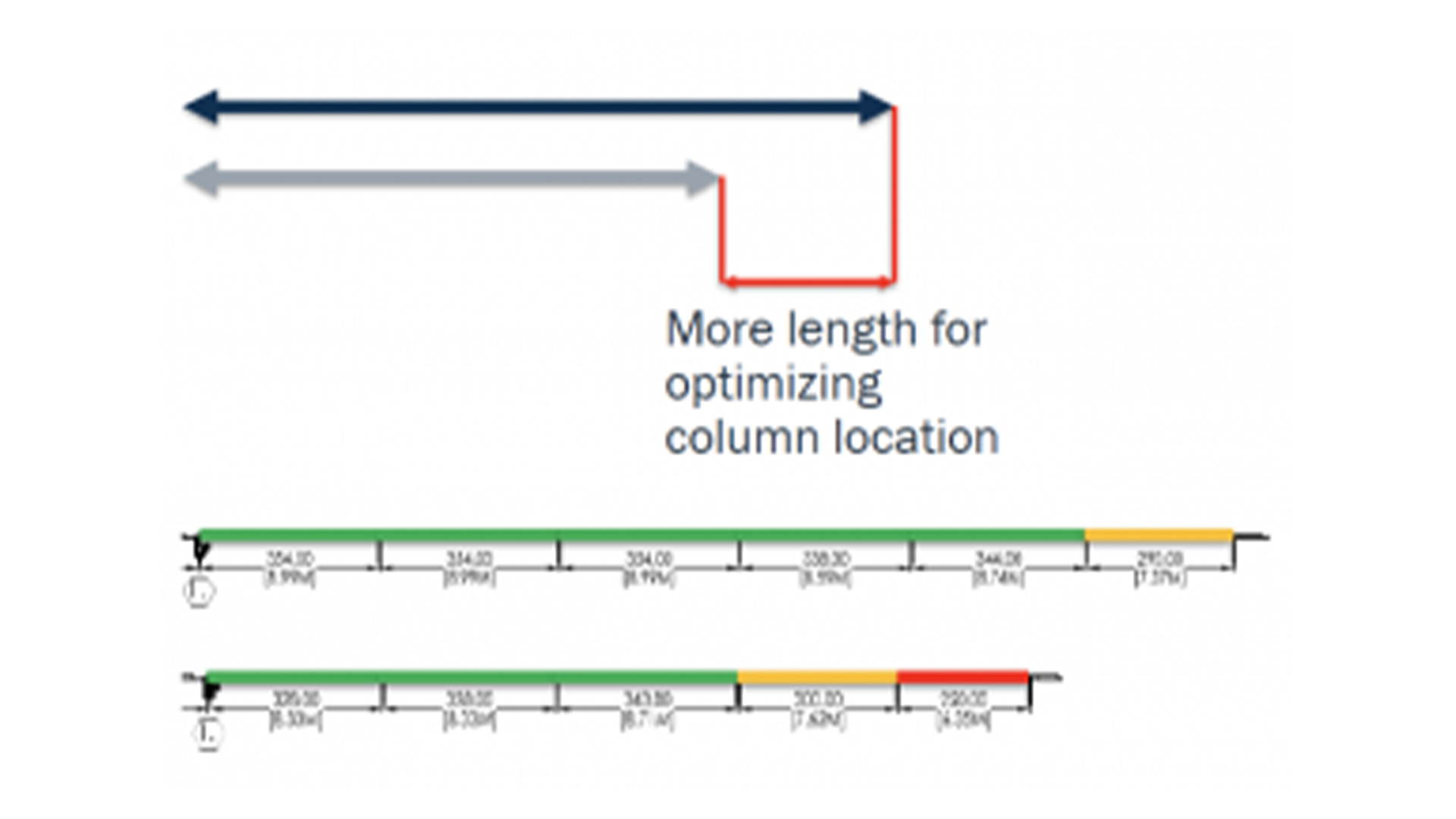
During the design phase of a utility-scale photovoltaic (PV) solar power plant, maximizing site coverage leads to the optimization of power yield – and there are a wide range of tools in a PV power plant designer’s tool belt to help accomplish this mission.
Customizing module row length is one tool. It can help PV plant developers, owners, project managers, financial analysts, and EPCs get a clearer picture of how to optimize site use, engage in minimal grading and, most importantly, boost energy yield.
By leveraging a four-string tracker row as opposed to a more traditional three-string row, the overall cost per watt of each individual tracker row can be reduced. Such a configuration may not be possible for every PV plant project, but it can offer an option to more cost-effectively utilize tracker components and reducing overall row count to get the most out of a fixed amount of DC watts for your site.
Extending Module Rows – A More Flexible Design Choice
By considering the extension and customization of module row lengths early on in a PV plant project, developers can define the most efficient design for a unique site – and the project’s unique budget constraints. It is important to understand the module string size range as early as possible to define the optimal modules per tracker row.
It’s helpful to think of extended row design concepts in terms of a few key metrics. By extending total length, PV plant projects can often also increase modules per post (or more generally meters per post). This is a key metric used to determine the cost efficiency of a tracker structure design.
Long Row Design Increases Meters per Column while Minimizing Required Components
In particular, meters per post can be a tremendous measure of efficiency and cost-effectiveness since it indicates how well the tracker structure utilizes foundations and their associated costs. Since foundations are a high-cost component in the total tracker cost stack they are a focus in the design process. And choosing a four-string configuration can typically allow PV plant projects to boost that metric.
Four-string rows also offer more row length for optimizing post location, meaning the tracker designer has more room along the row to find a post position that optimizes the tube span while avoiding interferences with module clamps or tube couplers.
This improved flexibility to optimize column location results in a greater total quantity of maximized spans along the row. And all of these maximized tube spans mean more meters per column, meeting the original design objective.
Further, when you compare a standard 3-string row to a 4-string row you are increasing the module count per row by 33%. Assuming you have a fixed DC capacity, you would reduce your total row count across the PV plant by a similar percentage. Since the motor count per block is fairly independent of row length this results in nearly a 33% increase in the DC power per motor.
There are also a number of components across the row that are required in a fixed count (dampers, gear racks, drivelines, etc.). Reducing the row count by nearly 33% results in an equivalent reduction of these “fixed count” components, and amortizes their cost across more DC power per row.
It’s simple. By customizing module row length, plant designers and planners can flexibly and cost-effectively increase the number of modules and adapt to match both plain terrain and challenging site geometry.
The Benefits of Customizing Module Row Length
By leveraging custom module row length on a PV plant site, you can decrease overall build time and cost, and, ultimately, increase plant profitability.
By utilizing a more flexible design choice via utilization of longer rows, you can:
- Reduce overall row count, reducing “fixed count” materials and their costs
- Optimize column location to more flexibly locate them, maximize tube span and avoid interferences
- Minimize the meter per column metric and utilize foundations more efficiently
- Reduce motor count and allow them to drive up to 33% more DC MWs
- Create greater power density thanks to fewer, larger motor blocks
- Experience a tracker cost reduction of between 2 and 6% based on unique site characteristics
The Proof Is in the PV Plants
Don’t just take our word for it. The proof is in the PV plants.
On a recent 700 MWdc project featuring approximately 1,700,000 modules (405 W power) using a row design of approximately 104 modules instead of 81, it was found that:
- Increasing module row length by 23 modules per row resulted in an upfront cost savings of $6.3 million.
- Plant resiliency was increased by eliminating extra components. In this case, more than 300 fewer motors were needed with the final optimized design, reducing the risk of component failure. Fewer motors also means reduced wiring, trenching, and labor expenses. With plants now designed to run over the course of three decades or more, this is critical.
- With help from engineers at ARRAY, the number of modules per foundation, a measure of the supporting posts that go into the ground to support each module row, dropped substantially. In this case, almost 20,000 fewer foundations were required, which was estimated to bring a cost savings of $3.9 million without sacrificing structural integrity.
- A surprising project budget savings was produced by the overall number of fasteners required for ARRAY’s DuraTrack when compared to the competition. ARRAY’s innovative single-bolt module clamp required over 3 million fewer fasteners than the competitive offering. This will result in a significant labor cost savings as well.
Check out this Array Webinar Unlocking Utility-Scale Solar Returns with Extended Module Rows from our archives.
Four-string configurations aren’t a “new product” or over-complicated solution – they’re simply a way for ARRAY to help PV plant projects get the most out of our industry-leading DuraTrack® HZ v3 single-axis tracker.
ARRAY is committed to serving as a flexible, trusted advisor to each unique PV plant project to ensure that it achieves the most optimal design and energy yield possible. Our four-string offering is unique, and it gives you additional tools in determining the best course of action for your unique needs and site.
ARRAY’s longer module row solution is about adding another tool to the arsenal of PV plant developers and owners and empowering you to find your ideal solution.
To learn more about how ARRAY Technologies can help you make the most of your site by partnering with you to optimize site design, customize module row length, and use the best software and trackers in the industry, register to attend Unlocking Utility-Scale Solar Returns with Extended Module Rows HERE on March 11, 2021 at 2pm ET / 11am PT.
Click here for other articles by this author